Choosing between rubber vs steel tracks can be confusing for skid steer owners. Which type will provide the best performance for your needs?
Rubber tracks are known for their comfort and lower ground damage, while steel tracks offer superior durability in rough terrain. This article breaks down the pros and cons of each to help you make the right choice.
Let’s dive into the key differences between rubber and steel tracks.
What Are Rubber Tracks and How Do They Work?
Rubber tracks have become an increasingly popular choice for skid steers and other heavy machinery, thanks to their exceptional performance across a wide range of surfaces. These tracks offer a smooth and comfortable ride, making them particularly suitable for applications where ground conditions are uneven or soft. Additionally, rubber tracks are gentle on the surface they traverse, which is ideal for work on delicate areas such as lawns, pavements, and other sensitive surfaces that require careful handling to avoid damage.
The construction of rubber tracks is also noteworthy. They are typically made from high-quality, reinforced rubber compounds that are specifically engineered to withstand the rigors of daily use. This design not only enhances their durability but also helps to reduce noise and vibration, making them a more pleasant and efficient option for operators. Whether it’s a construction site with soft, muddy ground or an urban environment where noise levels need to be kept to a minimum, rubber tracks are often the preferred choice. Their versatility and performance make them a valuable addition to any fleet of machinery.
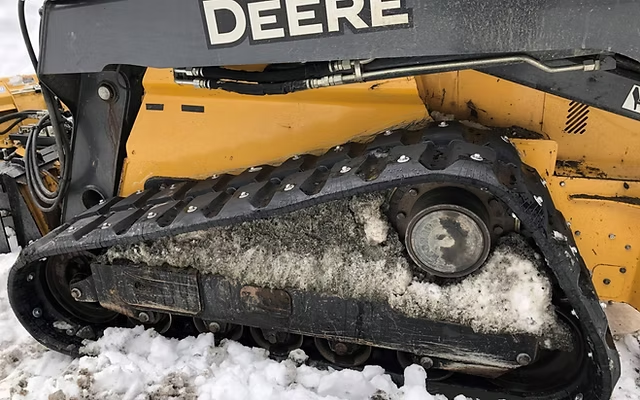
What Are Steel Tracks and How Do They Work?
On the other hand, steel tracks are designed with extreme durability in mind, making them the go-to choice for heavy-duty applications and challenging conditions. Constructed from robust steel links, these tracks provide exceptional traction, especially in rough terrains such as muddy, rocky, or uneven surfaces. This makes them highly effective in environments where grip and stability are crucial.
While steel tracks may be less gentle on surfaces compared to their rubber counterparts, they are engineered to handle significantly more weight and deliver superior traction. This ruggedness and strength make them ideal for construction projects that demand consistent and powerful performance, ensuring that machinery can operate efficiently even in the most demanding conditions. Whether it’s moving heavy loads or navigating difficult terrain, steel tracks are built to withstand the test of time and deliver reliable results.
Advantages of Rubber Tracks
Rubber tracks have garnered widespread favor among many operators due to the multitude of benefits they offer. These tracks are renowned for their quiet operation, significantly reducing noise levels compared to their steel counterparts. This makes them particularly suitable for environments where minimizing noise is crucial, such as urban areas or near residential neighborhoods.
Moreover, rubber tracks are designed to minimize ground damage. Their gentle touch on surfaces ensures that delicate terrains like lawns, gardens, and paved areas remain unscathed, making them an ideal choice for landscaping, gardening, and construction projects in sensitive environments. The smooth ride provided by rubber tracks is another key advantage. Their flexible nature allows them to conform to uneven surfaces, reducing vibrations and providing a more comfortable experience for the operator. This not only enhances the overall usability of the machinery but also reduces operator fatigue during long hours of operation.
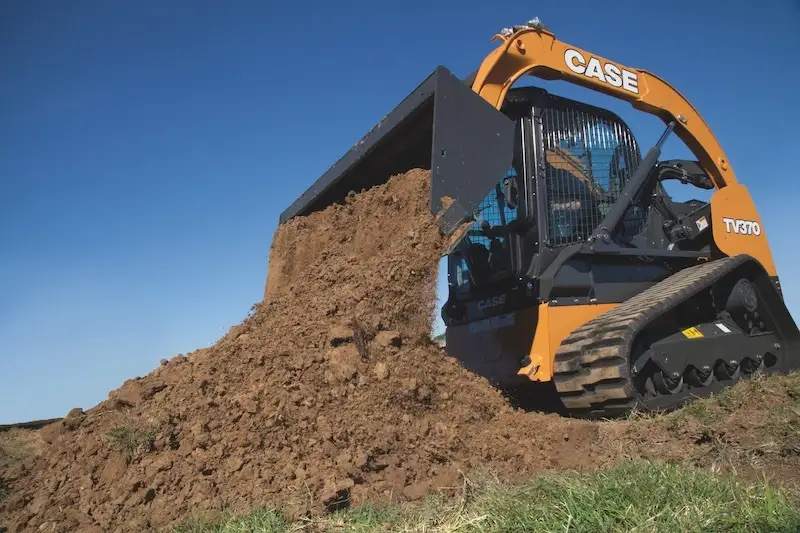
In summary, the combination of noise reduction, minimal ground damage, and a smoother ride makes rubber tracks a preferred choice for a wide range of applications, especially those that require sensitivity to the ground and a comfortable operating experience.
Advantages of Steel Tracks
When it comes to heavy-duty work and tough environments, steel tracks are often the preferred choice for many operators. These tracks are specifically designed to thrive in extreme conditions, providing long-term durability and superior traction in harsh terrains such as rocky, muddy, or uneven surfaces. Whether it’s navigating through rugged landscapes or operating in demanding construction sites, steel tracks offer the strength and reliability needed to handle heavy loads and maintain high performance.
The robust construction of steel tracks, made from durable steel links, ensures that they can withstand the rigors of continuous use in challenging environments. This makes them an ideal solution for projects that require consistent and powerful performance, even in the most demanding conditions. Operators can rely on steel tracks to provide the necessary support and stability, ensuring that their machinery operates efficiently and effectively, regardless of the terrain or workload.
In summary, steel tracks are a reliable and durable option for those working in tough environments. Their ability to provide superior traction, handle heavy loads, and maintain high performance makes them a valuable asset for any heavy-duty project.
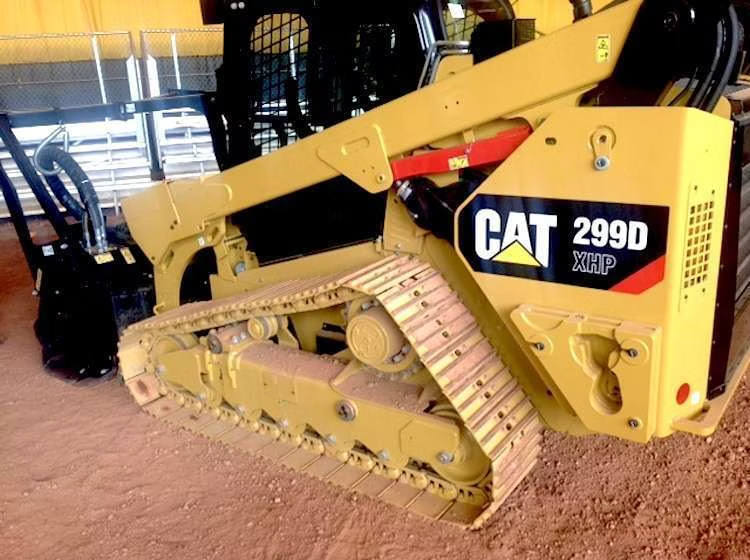
Comparison: Rubber vs Steel Tracks in Terms of Durability
When deciding between rubber and steel tracks, durability is a key factor to consider. Both types of tracks have their strengths and weaknesses, but they perform differently in various conditions.
Rubber tracks are known for their versatility and gentleness on surfaces. However, they are more susceptible to wear and tear in extreme conditions. For instance, when operating in environments with sharp rocks, jagged debris, or abrasive surfaces, rubber tracks can degrade more quickly. Despite this, their impact on the ground is significantly less damaging compared to steel tracks. This makes rubber tracks a preferred choice for applications where preserving the underlying surface is crucial, such as working on lawns, paved roads, or in urban settings.
On the other hand, steel tracks are engineered for longevity and resilience. They are built to withstand the harshest conditions and heavy-duty use, making them an ideal choice for environments with rough terrain, such as rocky landscapes, muddy construction sites, or areas with sharp objects. Steel tracks are designed to endure the rigors of continuous operation without significant degradation. However, their toughness comes with a trade-off: they can be more abrasive on surfaces, particularly on paved areas, which may lead to increased wear and damage over time.
In summary, while rubber tracks offer a gentler touch on surfaces and are suitable for less demanding environments, steel tracks provide superior durability and resilience in harsh and heavy-duty conditions. The choice between the two ultimately depends on the specific requirements and conditions of the job at hand.
Cost Considerations: Rubber vs Steel Tracks
When it comes to choosing between rubber and steel tracks, cost is a crucial consideration that can significantly impact the overall value and long-term savings.
Rubber tracks are typically more affordable at the outset, making them an attractive option for those looking to minimize initial expenses. However, they may need to be replaced more frequently, especially when used in harsh or demanding conditions. This can lead to additional costs over time, as frequent replacements can add up.
In contrast, steel tracks come with a higher initial price tag. This upfront investment can be a deterrent for some, but it’s important to consider the long-term benefits. Steel tracks are designed to be highly durable and resilient, often lasting much longer than rubber tracks in tough environments. As a result, they require fewer replacements, which can lead to significant cost savings over the life of the machinery.
Operators should not only focus on the initial purchase price but also take into account the total cost of ownership, including maintenance and replacement costs. While steel tracks may seem more expensive initially, their longer lifespan and reduced need for replacements can result in lower overall costs in the long run. This makes them a cost-effective choice, particularly for heavy-duty applications and environments where durability is paramount.
In summary, while rubber tracks offer a lower initial cost, steel tracks can provide greater long-term value through their durability and reduced maintenance needs. It’s essential to weigh both the upfront and ongoing costs to make the most informed decision.
Which Type of Track is Best for Different Applications?
Selecting the appropriate track type for your skid steer largely hinges on the specific tasks and environments in which it will be utilized.
For lighter-duty tasks and work on softer surfaces, such as landscaping, gardening, or working on lawns and delicate terrains, rubber tracks are the optimal choice. They offer a smooth ride, minimize ground damage, and are particularly well-suited for applications where preserving the underlying surface is crucial. Additionally, in urban environments or areas with hard surfaces like paved roads and sidewalks, rubber tracks provide a more comfortable operating experience and reduce the risk of surface damage.
Conversely, steel tracks are designed to excel in more demanding and rugged environments. They are ideal for heavy-duty construction projects, off-road work, and any scenario where the terrain is particularly challenging, such as rocky, muddy, or uneven surfaces. Steel tracks offer superior traction and durability, enabling machinery to handle heavy loads and maintain high performance even in the most arduous conditions. Their robust construction ensures longevity and reliability, making them a reliable choice for operators working in tough environments.
In summary, the decision between rubber and steel tracks should be guided by the nature of your work and the environments in which your skid steer will operate. Rubber tracks are perfect for lighter tasks and sensitive surfaces, providing comfort and minimal ground impact. Steel tracks, on the other hand, are built for heavy-duty applications and demanding terrains, offering the traction and durability needed to get the job done efficiently and effectively.
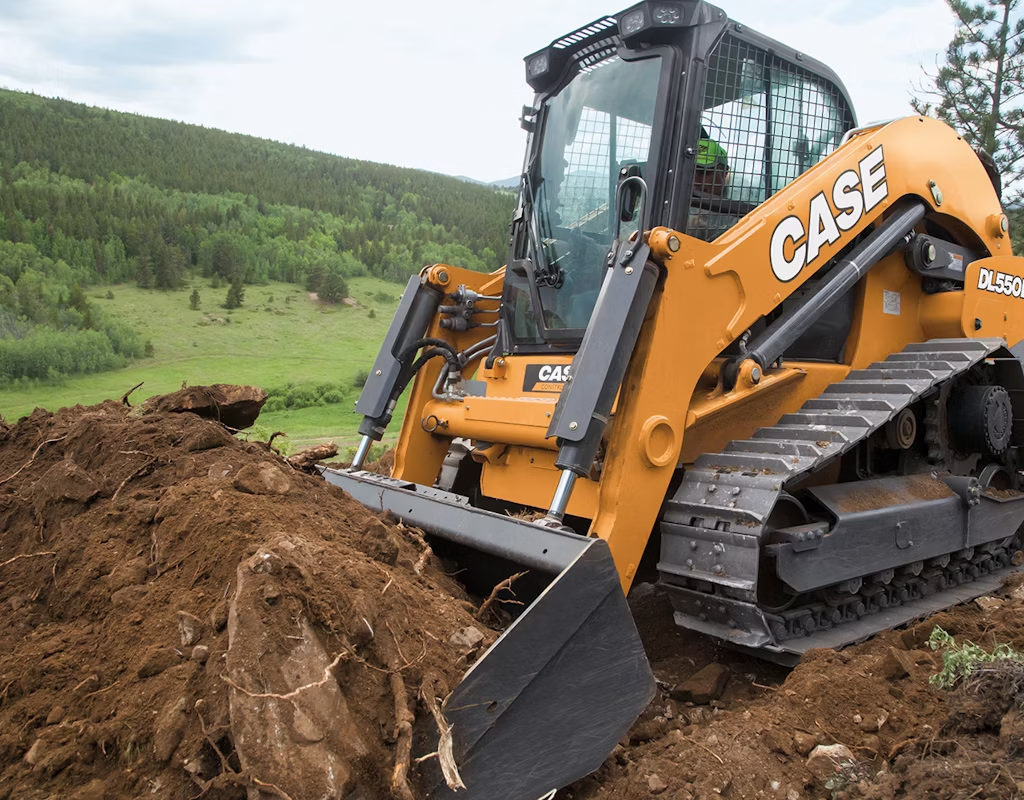
Maintenance and Repair of Rubber vs Steel Tracks
The maintenance requirements for rubber and steel tracks differ significantly, and understanding these differences is crucial for maximizing their performance and longevity.
Rubber Tracks: Rubber tracks are more susceptible to damage from sharp objects and rough handling. To maintain their integrity, it’s important to avoid contact with debris, rocks, and other sharp items that could cause punctures or tears. Regular inspections should focus on checking for cracks, cuts, and signs of excessive wear. These issues can compromise the track’s durability and performance, so addressing them promptly is essential. Additionally, keeping the tracks clean and free from debris can help prevent damage and extend their lifespan.
Steel Tracks: Steel tracks, while more durable, require a different set of maintenance practices. Regular inspections are necessary to check for signs of rust, corrosion, and wear, particularly at the joints and connections. Rust can weaken the track’s structure, so applying a rust-preventative coating or lubricant can help mitigate this risk. Lubrication is also important to ensure smooth operation and reduce friction, which can extend the life of the track and its components. Keeping the tracks clean and free from dirt and moisture is another key aspect of maintaining steel tracks.
General Maintenance Tips: Regardless of the type of track, regular inspections are vital. This includes checking for any signs of damage, wear, or misalignment. Addressing issues early can prevent minor problems from becoming major repairs. Additionally, proper storage conditions, such as keeping tracks clean and dry, can significantly extend their lifespan. For rubber tracks, avoiding prolonged exposure to direct sunlight and extreme temperatures can help prevent premature aging and degradation. For steel tracks, ensuring they are stored in a dry environment can reduce the risk of rust.
In summary, while rubber tracks require careful handling to avoid punctures and wear, steel tracks demand regular inspection and maintenance to prevent rust and ensure longevity. By understanding and addressing the specific maintenance needs of each type of track, operators can maximize their performance and extend their lifespan, ultimately saving time and money in the long run.
Краткое содержание
In conclusion, choosing the right type of track for your skid steer is essential for efficiency and performance.
Rubber tracks are better for comfort and lighter-duty work, while steel tracks offer more durability and traction for harsh environments.
Make an informed decision based on your operational needs and terrain conditions.