Understanding the parts of an excavator helps you grasp how it operates and aids in selecting the right model for your needs. Knowing these components can also simplify maintenance and repair tasks.
The main parts of an excavator include the undercarriage, house, boom, arm, bucket, and hydraulics. Each part plays a vital role in the performance and versatility of the machine, enabling it to perform various tasks efficiently.
Let’s explore each of these crucial parts in more detail and understand their role in making an excavator work.
Undercarriage of an Excavator
The undercarriage serves as the backbone of an excavator, bearing its substantial weight and ensuring stability throughout various operations. It plays a pivotal role in facilitating mobility and enhancing performance across a wide range of terrains, from rugged and uneven landscapes to relatively smooth and solid surfaces.
An excavator’s undercarriage is an intricate assembly of key components, including the tracks or wheels, track frame, and final drive. These elements collaborate seamlessly to provide the machine with the necessary traction and balance, allowing it to navigate smoothly over rough and uneven ground. The tracks, in particular, offer exceptional grip on soft or unstable surfaces, enabling the excavator to maintain its footing and carry out tasks effectively. On the other hand, wheels are better suited for smoother, more solid terrains, where they can roll effortlessly and efficiently.
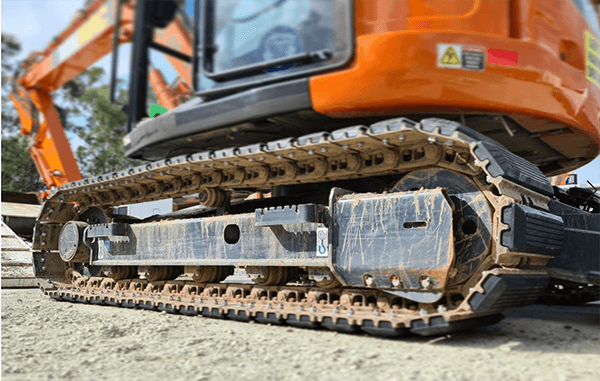
The undercarriage is further composed of several integral parts: the track chain, sprockets, rollers, and idlers. Each of these components contributes to the overall functionality and robustness of the undercarriage. The tracks, with their interlocking design, provide a continuous surface that distributes the excavator’s weight evenly, reducing ground pressure and minimizing the risk of sinking or getting stuck. The sprockets, rollers, and idlers work in tandem to guide and support the tracks, ensuring smooth movement and proper alignment.
Given its constant exposure to harsh working conditions, such as dirt, debris, and heavy loads, the undercarriage is particularly susceptible to wear and tear. Therefore, proper maintenance is of utmost importance to ensure its durability and longevity. Regular inspections should be conducted to check for signs of wear on the tracks, rollers, and other components. By promptly addressing any issues, such as loose or damaged parts, not only can optimal performance be maintained, but also costly repairs and potential downtime can be effectively prevented. This proactive approach to undercarriage maintenance is crucial for maximizing the efficiency and reliability of the excavator in the long run.
The House of an Excavator
The house constitutes the upper structure of the excavator, perched atop the undercarriage like a command center. It serves as a protective and functional enclosure for a host of vital components, including the operator’s cab, engine, and hydraulic systems, which are the lifeblood of the excavator’s operations.
Within the house, you’ll find the cab, engine compartment, counterweight, and slew ring, all meticulously designed to work in harmony. One of the most remarkable features of the house is its ability to rotate 360 degrees independently of the undercarriage. This full-circle rotation capability is a game-changer, allowing the excavator to operate with unparalleled efficiency and flexibility, as it can easily pivot to face any direction without needing to reposition the entire machine.
The operator’s cab is the nerve center of the excavator, where the machine’s fate is steered. It’s a compact yet ergonomically designed space that houses an array of joysticks, levers, and other intuitive controls. These controls are strategically placed within easy reach of the operator, enabling precise and effortless manipulation of the excavator’s various functions. From the comfort of the cab, the operator can skillfully guide the excavator through complex tasks, making it the cockpit from which the excavator’s power is harnessed.
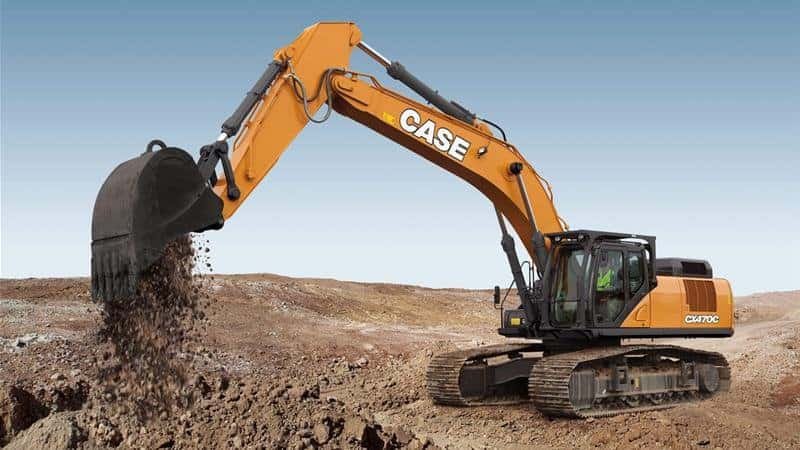
Positioned strategically at the rear of the house, the counterweight plays a crucial role in maintaining balance. When the excavator is engaged in the arduous task of lifting heavy loads, the counterweight acts as a stabilizing force, preventing the machine from tipping over. It’s like a counterbalancing scale, ensuring that the excavator remains steady and secure, no matter the weight it’s handling.
And then there’s the slew ring, a marvel of engineering that allows the upper structure to rotate with silky smoothness. This rotational mechanism is not just a mechanical feat; it’s the key to the excavator’s versatility. Whether it’s digging a trench, loading a truck, or performing delicate excavation work in tight spaces, the slew ring enables the excavator to adapt to a wide variety of digging tasks with ease. It’s the pivot point that transforms the excavator into a multi-purpose powerhouse, capable of tackling any job that comes its way.
Boom of an Excavator
The boom is a pivotal component of an excavator, acting as its extended arm that significantly enhances the machine’s operational capabilities. It enables the excavator to carry out digging and lifting tasks at a multitude of depths, reaching areas that would otherwise be inaccessible. This versatile extension is the excavator’s key to accessing both shallow and deep excavation sites with precision and ease.
Connected securely to the house, the boom is powered by robust hydraulic cylinders, which are the driving force behind its movements. These cylinders grant the boom the necessary reach and strength to undertake a diverse array of tasks. Whether it’s excavating deep trenches for pipeline installations or hoisting heavy materials to elevated construction sites, the boom is at the forefront of the excavator’s functionality.
Excavators are designed with various boom configurations to suit different job requirements. The two primary types are straight and curved booms, each with its unique set of advantages. A straight boom is engineered for deep digging applications, providing a direct and powerful reach that allows the excavator to penetrate deep into the ground with minimal resistance. Its linear design ensures that the force exerted is concentrated and efficient, making it the go-to choice for tasks that demand depth.
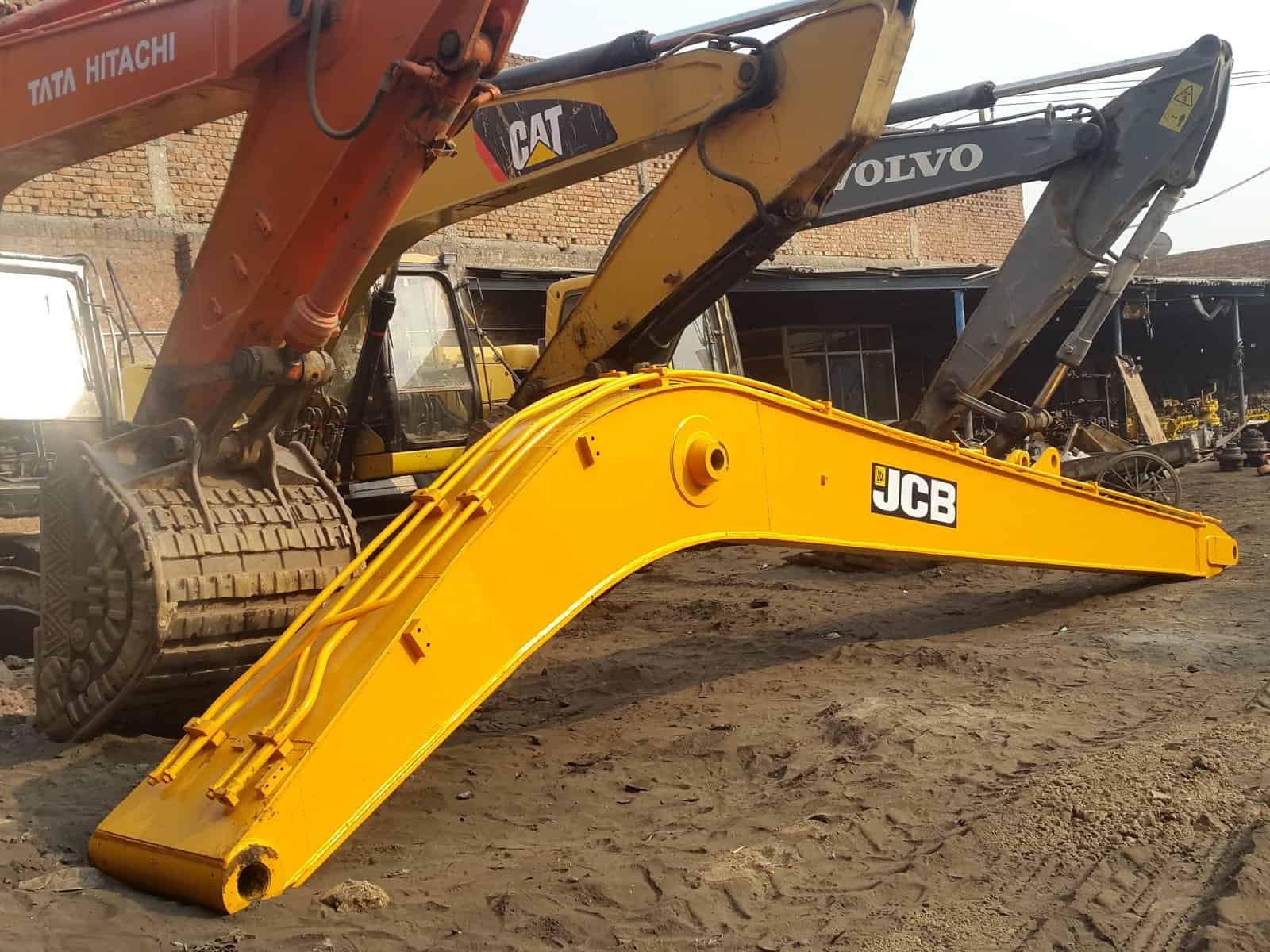
On the other hand, a curved boom is designed with maneuverability in mind. Its contoured shape enables the excavator to work effectively in confined spaces, such as urban construction sites with limited room for movement or areas with obstructions. The curvature allows the boom to navigate around obstacles and reach tight corners, making it an invaluable asset for precision work in restricted environments.
To ensure the boom operates at peak performance, regular checks and maintenance are indispensable. The hydraulic components, in particular, require meticulous attention. These components are responsible for the controlled extension and retraction of the boom, and their proper functioning is crucial for the excavator’s accuracy and safety. By conducting routine inspections and timely maintenance, potential issues such as leaks, wear, or malfunctions can be identified and addressed promptly. This proactive approach not only prolongs the life of the boom but also guarantees that the excavator remains a reliable and efficient workhorse on any job site.
Arm of an Excavator
The arm, also known as the stick, serves as the crucial link between the boom and the bucket in an excavator. It plays a vital role in extending the reach of the bucket, enabling the excavator to execute precise digging and lifting maneuvers with remarkable accuracy. This extension not only enhances the machine’s reach but also allows for a wide range of motion, making it an indispensable component for various excavation tasks.
Driven by powerful hydraulic cylinders, the arm boasts an impressive level of adjustability. It can be fine-tuned to different lengths and angles, which significantly boosts the excavator’s adaptability, especially in challenging environments. Whether working in tight, confined spaces where every inch of movement counts, or delving into great depths for extensive digging projects, the arm’s versatility is a game-changer. It empowers the excavator to navigate complex terrains and execute tasks that would be otherwise difficult or impossible to achieve.
The arm’s extensive range of motion and its ability to pivot are fundamental to the excavator’s efficient operation. When it comes to digging in narrow trenches or undertaking tasks that demand pinpoint precision, the arm’s functionality becomes paramount. Its capacity to extend and retract with ease grants the operator full control over the depth and angle at which the bucket operates. This level of control is essential for achieving the desired results, whether it’s excavating a foundation, grading a slope, or loading materials onto a truck.
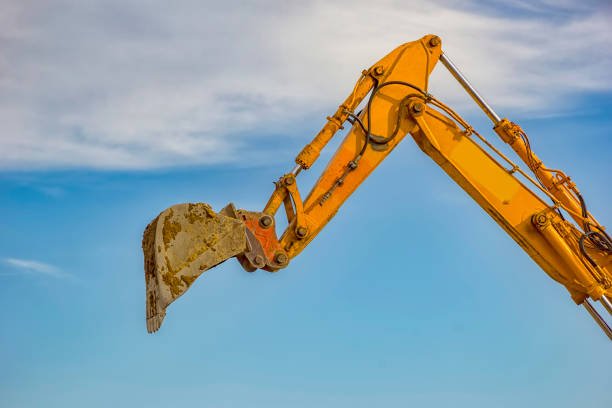
To maintain the arm’s optimal performance and ensure the excavator operates smoothly and responsively, regular inspections of the arm and its hydraulic systems are of utmost importance. These checks help identify any signs of wear, damage, or potential malfunctions in a timely manner. By addressing these issues promptly, operators can prevent costly repairs, minimize downtime, and keep the excavator running at peak efficiency. In essence, the arm, with its hydraulic-powered capabilities, is the excavator’s dynamic limb that brings precision, flexibility, and power to every job site.
Bucket of an Excavator
The bucket stands as the excavator’s primary workhorse, tasked with the essential functions of digging, lifting, and scooping a wide array of materials. It is available in an extensive range of shapes and sizes, each meticulously designed to meet the specific demands of diverse job sites. From the broad and shallow buckets ideal for light grading tasks to the deep and narrow ones perfect for trench digging, the bucket’s versatility is a testament to its importance in the excavation process.
Excavator buckets are engineered to tackle a multitude of tasks with precision and efficiency. Whether it’s the deep excavation required for foundation work, the delicate grading needed for landscaping projects, or the robust material handling essential for construction sites, the bucket is at the forefront of these operations. A key feature of the bucket is its teeth, which are the sharp, rugged components that make initial contact with the ground. These teeth are indispensable for breaking through tough soil, compacted clay, or even rocky terrain, providing the excavator with the necessary bite to get the job done.
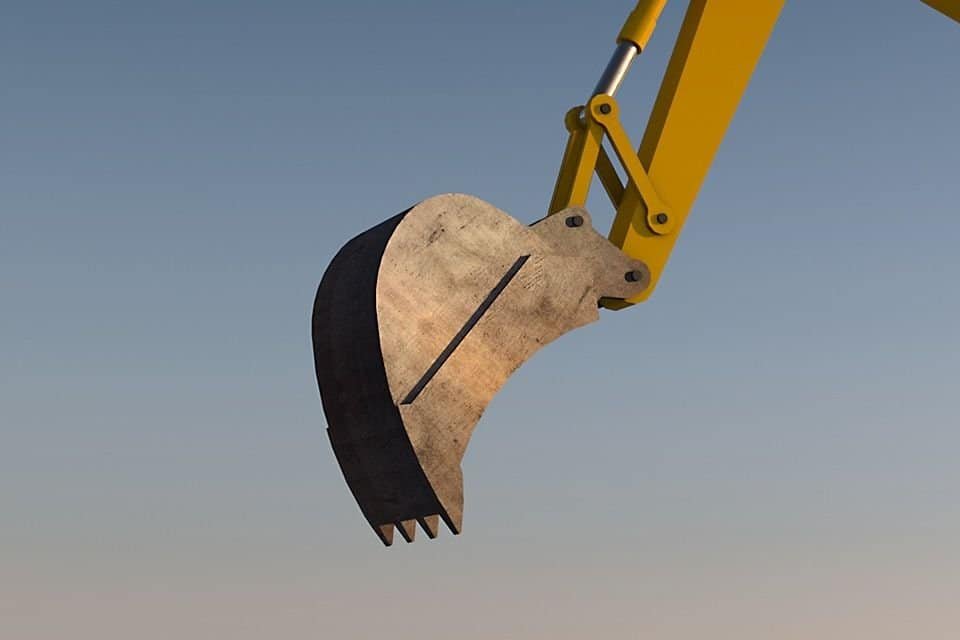
The customization options for buckets are vast, allowing operators to equip their excavators with the most suitable tools for the task at hand. The type of teeth or blades attached to the bucket can be tailored to match the material being excavated. For instance, a heavy-duty bucket, armed with robust, reinforced teeth, is specifically designed to penetrate and excavate through the most challenging terrains, such as rocky outcrops or hard-packed earth. In contrast, a general-purpose bucket, with its more standard teeth configuration, excels in handling softer materials like loose soil or sand, making it a versatile choice for a wide range of applications.
To ensure the excavator remains a reliable and effective tool, regular maintenance of the bucket’s teeth and edges is crucial. This upkeep not only preserves the bucket’s cutting efficiency but also minimizes the wear and tear on the arm and boom during operation. By keeping the teeth sharp and the edges clean, the excavator can maintain its digging prowess, reducing the strain on the machine’s components and prolonging its overall lifespan. In essence, the bucket, with its array of customizable features and robust design, is the excavator’s frontline implement, ready to tackle any excavation challenge with power and precision.
Hydraulic System of an Excavator
The hydraulic system is the powerhouse behind nearly every movement an excavator makes, essentially serving as the machine’s beating heart that drives its functionality. It’s responsible for animating the boom, arm, and bucket, enabling the excavator to carry out its diverse range of tasks with precision and strength.
At the core of the hydraulic system are the hydraulic cylinders and motors, which act as the transformative elements. They take the pressure generated by the hydraulic fluid and convert it into mechanical force. This conversion is what gives the excavator the ability to lift heavy loads with ease, dig deep into the earth with power, and rotate its upper structure with smoothness and control. It’s a symphony of engineering that turns fluid pressure into tangible, productive motion.
The hydraulic system itself is a complex assembly of several integral components, each playing a crucial role in the machine’s operation. The pump is the starting point, generating the pressure that propels the hydraulic fluid through the system. Valves act as the traffic controllers, directing the flow of fluid to where it’s needed most, ensuring that each component receives the right amount of pressure at the right time. Cylinders are the actuators, expanding and contracting to move the excavator’s parts, while the hydraulic fluid is the lifeblood, transferring energy throughout the system.
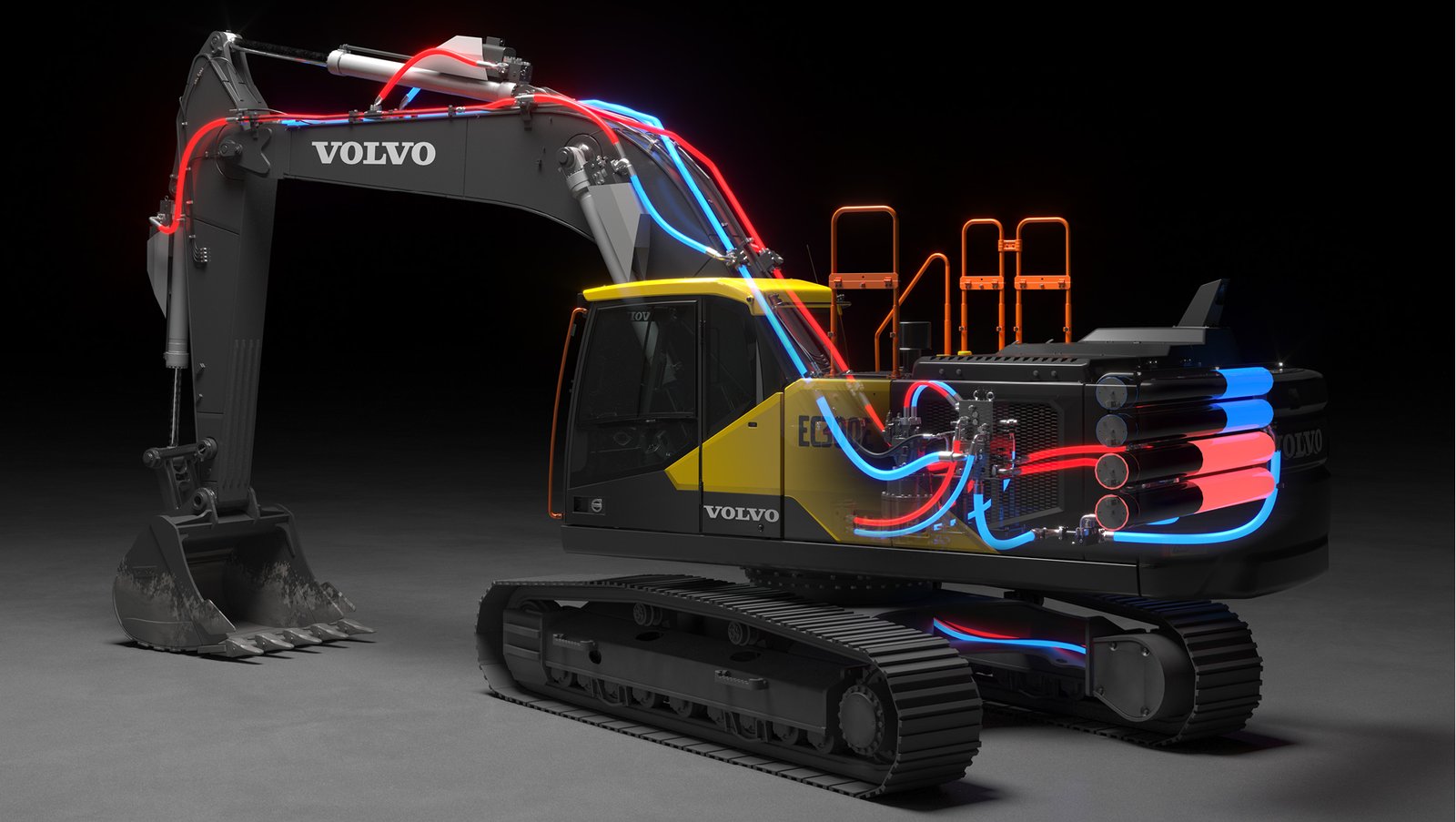
Maintaining the hydraulic system is not just important—it’s imperative for the excavator’s performance and longevity. Regular checks of the hydraulic fluid levels are essential to ensure that the system is adequately lubricated and powered. Replacing filters is equally critical, as it helps to keep contaminants out of the system, which could otherwise lead to clogs, reduced efficiency, and potential damage. By diligently monitoring these aspects, operators can prevent leaks, system failures, and the costly downtime that comes with them. A well-maintained hydraulic system means an excavator that runs smoothly, efficiently, and is always ready for the next job, making it an indispensable part of any construction or excavation project.
Operator’s Cab Parts of An Excavator
The operator’s cab is where the excavator operator controls the machine. It is designed for comfort and optimal visibility, providing a safe working environment.
The cab contains all the necessary controls, such as joysticks, pedals, and display panels. It is equipped with features like air conditioning, adjustable seating, and enhanced visibility.
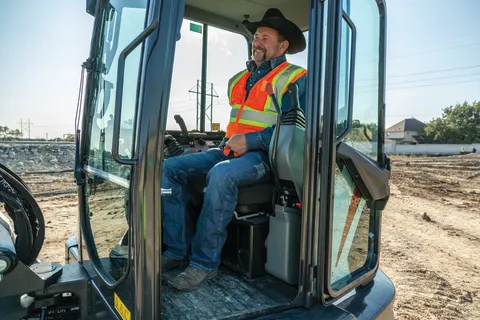
The operator’s comfort directly impacts productivity. A well-designed cab ensures that the operator has easy access to all controls and a clear view of the worksite. Modern cabs also include advanced displays for real-time monitoring of the machine’s performance and diagnostics. Safety features such as rollover protection and adjustable seating further enhance the overall experience.
Counterweight of an Excavator
The counterweight is essential for stabilizing the excavator during lifting and digging tasks. It helps to prevent tipping, particularly when the boom and arm are extended.
The counterweight is typically located at the rear of the excavator, balancing the forces created during operation. It is designed to provide counteracting force to the weight of the arm and bucket.
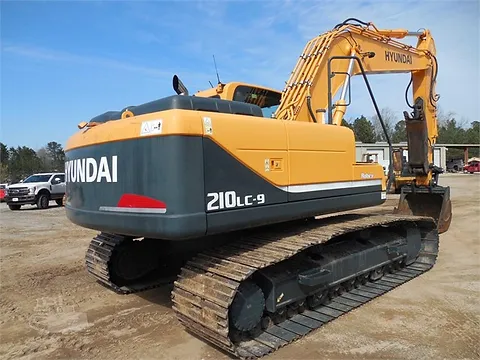
The weight of the counterweight depends on the excavator’s size and lifting capacity. A larger counterweight may be required for machines with higher lifting capabilities or extended booms. Maintaining the counterweight is important for safety and stability during operation, especially when performing heavy lifting tasks or working on uneven ground.
Summary:
Understanding the main parts of an excavator—from the undercarriage to the hydraulic system—can help you make informed decisions when purchasing or maintaining this powerful construction equipment.